在材料科学研究和工业检测中,金相分析是一项基础而关键的技术。其中,样品的制备过程,尤其是金相抛光机抛光后的表面质量,直接影响较终显微组织观察的清晰度与准确性。因此,对抛光后样品表面质量进行科学、系统的评估,是确保金相分析结果可靠的重要环节。
一、视觉观察法:初步判断表面状态
较直接的评估方式是通过肉眼或低倍显微镜进行视觉检查。优质抛光面应呈现均匀、无划痕、无麻点、无变形层的镜面效果。若表面存在明显划痕、雾状痕迹或局部凹陷,则说明抛光过程中可能存在操作不当、磨料选择不合适或冷却不足等问题。
二、光学显微镜检测:评估微观结构完整性
借助光学显微镜(OM)对抛光样品进行高倍放大观察,是评估表面质量的核心手段之一。优质的抛光样品应能清晰显示材料的真实组织结构,如晶界、析出相、夹杂物等,且无因机械变形引起的伪影。若组织模糊、晶界不清,可能是由于抛光过度或压力过大造成表层损伤。
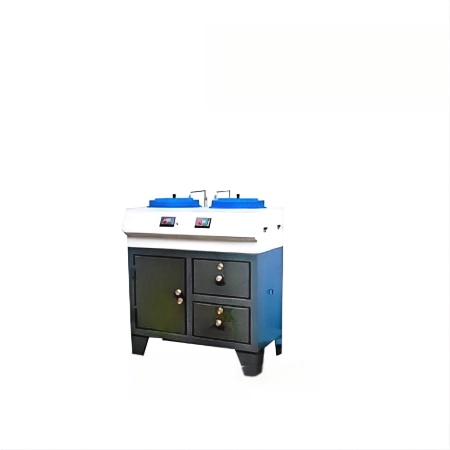
三、表面粗糙度测量:量化评价指标
采用表面粗糙度仪对抛光面进行Ra值(轮廓算术平均偏差)测量,是一种客观量化的评估方式。通常,金相抛光后的Ra值应控制在0.05μm以下,以满足高质量显微观察需求。数值越高,表明表面越粗糙,可能影响后续显微图像的分辨率与分析精度。
四、电子背散射衍射(EBSD)或扫描电镜(SEM)分析:深度验证晶体结构
对于要求较高的科研或制造领域,常使用扫描电镜或电子背散射衍射系统对抛光样品进行更深入的分析。这些技术能够检测材料表面晶体取向、晶格畸变等情况,从而判断是否存在因抛光导致的亚表面损伤或再结晶现象。
五、综合评分体系:建立标准化评估流程
为提升评估效率与一致性,部分实验室建立了基于图像处理软件的自动评分系统,结合划痕数量、表面光泽度、晶粒对比度等多维度参数,实现对抛光质量的自动化分级评定。
综上所述,金相抛光机抛光后样品表面质量的评估应从宏观到微观、从定性到定量多个层面展开。只有通过科学、系统的评估方法,才能确保金相分析结果的准确性和可重复性,为材料研究、工艺优化及质量控制提供坚实保障。